Debemos o podemos mezclar soldaduras libres de plomo con las que no lo son? Esta pregunta de mucha actualidad, tiene respuestas a favor y en contra, basadas en las experiencias de fabricantes de soldadura y ensambladores de productos electrónicos. La mezcla de soldaduras que contengan o no Plomo puede en la mayoría de los casos, ocasionar soldaduras poco robustas y confiables a largo tiempo.
Este artículo pretende documentar al lector sobre las bases teóricas de los procesos y propiedades de las soldaduras utilizadas para soldar componentes electrónicos, y soportar las conclusiones finales que nos permitan tener claridad al respecto de su elección y uso. La entrada en vigencia de la normativa RoHS ha puesto en evidencia problemas que se generan en los procesos de soldadura al suprimir el Plomo como metal componente de la soldadura.
Soldaduras para uso en electrónica.
Soldadura de Estaño-Plomo: Es la soldadura tradicional que ha sido usada por la mayoría de nosotros en los procesos de ensamble de circuitos electrónicos y que conserva en la actualidad un mercado importante en el sector. Las aleaciones más comerciales son la Sn60Pb40 y la Sn63Pb37, siendo esta última la más comercial por su bajo punto de fusión y acabado brillante en las soldaduras de circuitos impresos. Tiene un contenido del 63% de Estaño y 37% de Plomo y viene en presentación de rollos para componentes convencionales y en crema para componentes SMD.
Actualmente, algunos fabricantes estipulan su toxicidad en el empaque debido al contenido de Plomo.
Ventajas:
- Bajo costo comparado con otras aleaciones.
- Requiere una relativa baja temperatura. Usualmente en el rango de 183 ºC a 225 ºC.
- Apariencia brillante y fácilmente inspeccionable.
- Se extiende fácilmente sobre las superficies a soldar, pudiéndose utilizar esta característica como indicador del proceso de humedecido.
- El cambio de estado Humedecido-Fusión es fácilmente apreciable a simple vista.
- Su amplia ventana de trabajo permite controlar fácilmente los parámetros del proceso de soldadura.
- Si se cumplen las condiciones del proceso de soldadura, las uniones resultantes tienen la fortaleza necesaria para garantizar la confiabilidad a largo tiempo del producto final.
- Su uso en componentes SMD permite su centrado automático una vez floten sobre la soldadura fundida, debido a sus altas características de humedecido y tensión superficial.
- Fácil proceso de retrabajo.
Desventajas:
- Está orientada a desaparecer de circulación debido a la toxicidad por su contenido de Plomo y a la entrada en vigencia desde Julio de 2006, de la normativa RoHS que prohíbe el uso de Plomo en ensambles electrónicos.
Soldaduras libres de plomo: Existe una gran variedad de soldaduras que no contienen plomo como las aleaciones SnAg3.5 y Sn96.5Ag3Cu0.5 (SAC 305) entre otras, con temperaturas de fusión entre 217ºC y 227ºC siendo la SAC 305 la más usada en la actualidad en los procesos manuales e industriales de soldadura de componentes electrónicos. Usualmente utilizan el color verde en sus empaques y traen impreso distintivos alusivos a su amigabilidad con el ambiente.
Ventajas:
- Amigable con el ambiente.
- Aceptabilidad de los productos ensamblados en todos los mercados.
- Produce soldaduras robustas si se controlan estrictamente sus parámetros de operación.
Desventajas:
- Mayor costo debido al uso de Bismuto, Plata, Cobre y el reemplazo del plomo por Estaño, metales que son más costosos que el plomo.
- Requiere una temperatura mucho más alta en el proceso de soldadura. Usualmente en el rango de 217 ºC a 260 ºC.
- Apariencia opaca y más difícil de inspeccionar.
- Pobre humedecimiento.
- Ventana estrecha de trabajo, lo que requiere un control más preciso del proceso de soldadura.
- El centrado automático de los componentes SMD es pobre o no ocurre después de flotar cuando la soldadura alcanza su punto de fusión.
- El proceso de retrabajo es mucho más difícil y requiere herramientas compatibles.
Marco teórico:
Punto de fusión: El contenido de Estaño determina el punto de fusión de la soldadura. A mayor cantidad, menor temperatura de fusión requerirá la aleación resultante.
Tensión superficial: Este término lo podemos interpretar como la facilidad que tiene una sustancia para pegarse a otra cuando están en contacto. El metal fundido es un objeto difícil de manejar y su comportamiento se puede asimilar al del agua ya que si no encuentra a que “pegarse” se vuelve una bola debido a la tensión superficial que tiene en ese momento. Generalmente, cuando se cumplen las condiciones de un proceso de soldadura, la aleación pura se adhiere fácilmente a otra pero no a sus óxidos o si presenta contaminantes grasos.
Flux: Para evitar el rechazo a la adherencia, se deben limpiar las superficies antes de soldarlas. Esta es la función primaria del componente llamado Flux o fundente y que viene incorporado en el centro de un alambre de soldar o mezclado en una soldadura en crema para componentes SMD. Está compuesto básicamente por una sustancia desoxidante y un componente líquido que permite que la mezcla “humedezca” las superficies una vez el flux alcance su temperatura de fundición, siendo su valor mucho menor que la temperatura de fusión de la soldadura.
Algunos tipos de flux contienen aditivos cuya función es disminuir la tensión superficial entre la soldadura fundida y las superficies a soldar.
En la siguiente gráfica observamos el alambre de soldadura tradicional que contiene en su centro el fundente y en la gráfica central vemos un punto de soldadura en pasta aplicado, cuyas esferas están en contacto debido a la presencia del flux en su mezcla.
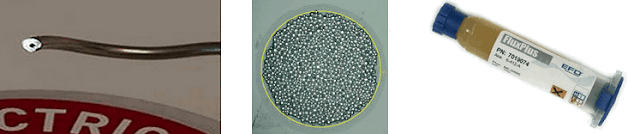
Activación del Flux: Al momento de fundirse el flux, se produce la evaporación de sus componentes líquidos, lo que corresponde al humo que vemos durante el proceso, y deja únicamente el componente activo en contacto con las superficies a soldar. Su función desoxidante está ahora activada y continúa hasta que la soldadura alcance su punto de fusión, para lograr la adherencia de las partes a soldar.
Humedecimiento: Es la propiedad que tienen las sustancias en estado liquido como el flux y la soldadura fundida para fluir o regarse sobre las superficies a soldar.
Intermetálicos: Son las capas compuestas por la disolución en la soldadura fundida de los metales que componen los revestimientos de las superficies a soldar. Son estrictamente necesarios para obtener una soldadura robusta y desafortunadamente representan la parte mas frágil de la unión si no se forman adecuadamente. Algunas formaciones intermetálicas son mas fuertes que otras y deberíamos tenerlas en cuenta al momento de elegir una aleación para soldar.
Si la capa formada es muy delgada, puede ser un problema pero si es muy densa, es un determinante de defectos en la unión ya que la soldadura podría no adherir a sus propias capas intermetálicas y/o producir poros por los vacíos creados durante su proceso de formación.
La siguiente figura nos ilustra como está conformada la estructura de una soldadura SAC y otra de aleacion Sn63Pb37 con sus respectivos intermetálicos.
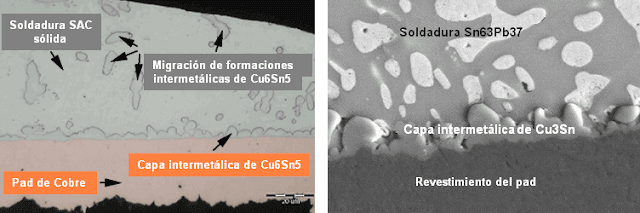
Los intermetálicos son normalmente formaciones cristalinas y químicamente estables una vez se han formado. Es la razón por la que una soldadura nunca se fracturará por su capa intermetálica, sino en sus uniones con las demás estructuras de la soldadura.
Importante: La formación de intermetálicos no está limitada al proceso de soldadura. La temperatura a que esté expuesto un producto durante su vida útil actúa como catalizador para la formación de intermetálicos al interior de una unión de soldadura. Los átomos de un metal pueden esparcirse aún en su estado sólido y aumentar la densidad de la capa intermetálica existente, con las consecuencias mencionadas.
Por lo anterior, los estudios de envejecimiento de una soldadura, usualmente están orientados a medir cuanta capa intermetálica cambiará de densidad y su efecto sobre la fortaleza mecánica de la unión de soldadura.
Procesos automatizados de soldadura: El control automático de los procesos de soldadura industrial de tarjetas electrónicas está basado en el uso de soldaduras y acabados compatibles de los circuitos impresos. Esto quiere decir que los fabricantes de soldadura y de equipos de control de sus procesos garantizan sus propiedades finales y funcionamiento, si la mezcla de aleaciones que intervienen en el proceso de soldadura es compatible. Por ejemplo, si tenemos tarjetas con acabados y componentes libres de Plomo, idealmente deberemos usar soldadura libre de Plomo para obtener soldaduras confiables a largo tiempo.
Por lo tanto, es fácil deducir que si no se cumplen esas condiciones, los resultados del proceso no se podrán garantizar y sus resultados finales deberán ser validados por el método de ensayo y error.
Compatibilidad de acabados de circuitos impresos, soldaduras y componentes: Desde mediados de 2006 cuando entró en vigencia la restricción RoHS sobre el uso de sustancias peligrosas en los productos, los fabricantes de insumos para los acabados de los circuitos impresos, de nuevos componentes electrónicos y de soldadura, fueron implementando su producción libre de Plomo. Sin embargo, considerando que por diversas razones para algunas categorías de componentes electrónicos, la migración total a su fabricación libre de Plomo se encuentra todavía en proceso de transición, se han definido los siguientes categorías para la compatibilidad de los componentes con los procesos de soldadura en términos metalúrgicos, procesos de soldadura y confiabilidad:
- Forward Compatibility: Esta calificación se refiere a los componentes tradicionales que han sido fabricados con revestimientos y/o el uso de soldaduras que contengan Plomo y su compatibilidad para ser ensamblados en circuitos impresos cuyos acabados y/o soldaduras sean libres de Plomo .
- Backward Compatibility: Esta calificación se refiere a los componentes actuales que han sido fabricados con revestimientos y/o soldaduras libres de Plomo y su compatibilidad para ser ensamblados en circuitos impresos cuyos acabados y/o soldaduras contengan Plomo .
Problemas al mezclar soldaduras no compatibles:
Asumiendo que el encapsulado de los componentes soporta los requerimientos de temperatura de la soldadura libre de plomo sin afectarlo, debemos tener en cuenta ciertas consideraciones al momento de mezclar características no compatibles de los elementos que intervienen en el proceso de soldadura.
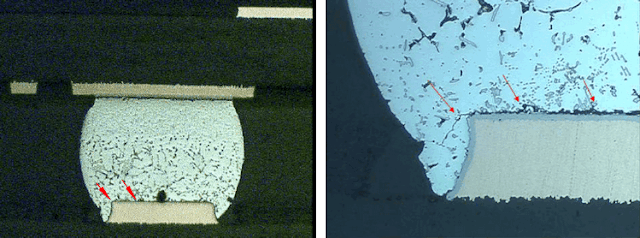
- Escenario I: En el caso de los componentes BGA, si aplicamos soldadura libre de plomo a los pads en el circuito impreso y las esferas del componente contienen Plomo se fundirán primero envolviendo la soldadura en pasta que todavía no se ha alcanzado su punto de fusión. Por lo tanto, el proceso de activación del flux de la soldadura libre de plomo ocurrirá directamente bajo la soldadura fundida insertándole burbujas producto de la evaporación del componente líquido de su flux, formando poros de un tamaño suficiente para debilitar la nueva unión de soldadura.
- Escenario II: En el caso contrario, donde las esferas del componente son libres de Plomo y aplicamos a los pads soldadura en pasta que contenga Plomo, esta se fundirá en primer lugar envolviendo la esfera del componente que todavía no ha alcanzado su temperatura de fusión ocasionando una soldadura fría si elegimos el perfil adecuado para la soldadura que contiene plomo.
Este problema puede solucionarse si se ajusta el perfil del proceso a un valor que permita fundir las dos aleaciones y obtener una mezcla homogénea. Sin embargo, esto requiere casi siempre el uso de una temperatura pico del proceso, mayor a la recomendada por el fabricante de la soldadura que indudablemente causará más burbujas que podrán a corto plazo, causar el defecto mencionado durante la vida útil de la tarjeta.
Estudio de las fallas en la microestructura de una soldadura BGA
La industria electrónica ha desarrollado estudios que le permitan elegir los materiales libres de Plomo y ajustar los procesos de fabricación y soldadura de componentes, para acelerar el proceso de erradicación total del Plomo de los ensambles electrónicos.
Las siguientes gráficas ilustran las fallas presentadas en las soldaduras de un componente, presentadas en una tarjeta ensamblada con las siguientes características:
- Tipo de componente: BGA con esferas de soldadura 5Ag3Cu0.5 (SAC 305).
- Soldadura en pasta: Soldadura corriente Sn63PB37
- Acabado de los pads del circuito impreso: Revestimiento por inmersión NiAu.
- Acabado de los pads del componente: SnNi
- Perfil de soldadura usado en el proceso: Para contenido de Plomo (SnPb)
- Test efectuado: Ciclos de choque térmico de -55C a +125C.
- Objetivo de la prueba: Evaluar la integridad de la soldadura a largo tiempo.
En la zona 3 observamos las siguientes regiones:
- Región A: Se observa la formación de delgadas plaquetas de intermetálicos Sn/Ag.
- Región B: Formaciones interdentríticas de Plomo en lugar de la matriz de Estaño presente en las zonas anteriores.
- Región C: Presencia de intermetálicos de SnAg de gran tamaño.
- Región D: Presencia de plaquetas intermetálicas de SnAg.
- Región E: Región interdentrítica de Plomo.
La zona 4 es la que estuvo en contacto directo con la soldadura SnPb, y se observa nuevamente una matriz de Estaño con escasas formaciones dentríticas, además de la presencia de intermetálicos de NiAg debido al acabado de los pads de la tarjeta y regiones de Plomo. También es evidente la zona de fractura en la interfaz de la soldadura con el PCB.
Estudios similares han demostrado que se puede obtener una soldadura resistente, si se ajusta el tiempo del perfil de temperatura empleado hasta lograr una mezcla homogénea de las aleaciones de soldadura. El problema es que dichos procedimientos no están documentados ni han sido tomados en cuenta en los procesos automáticos de soldadura, para este tipo de mezclas ya que han sido diseñados únicamente para la selección de un solo tipo de soldadura y por lo tanto ajustados a las características garantizadas por su fabricante. Los resultados obtenidos usando mezcla de soldaduras no compatibles deberán ser confirmados por complejos métodos de análisis como la microsección o el uso de microscopio electrónico etc.., que permitan garantizar al consumidor, la confiabilidad a largo tiempo requerida por el producto final.
Conclusiones:
Si necesariamente debemos usar algún componente que contenga plomo, deberemos soldarlo idealmente en un proceso aparte usando soldadura con plomo o avisar al fabricante para que no se ensamble al mismo tiempo que los demás componentes libres de plomo y se implemente su proceso de soldadura utilizando la soldadura compatible.
Si nuestro producto requiere ser ensamblado con una alta confiabilidad y robustez a largo plazo en sus soldaduras durante su vida útil o si debe cumplir con normativa RoHS, entonces no es aconsejable utilizar soldadura que contenga plomo, ni circuitos impresos que tengan acabados HASL con aleación Estaño-Plomo (SnPb) sobre sus pads.
Recomendaciones:
- Independientemente de los requerimientos de nuestra tarjeta al respecto, los circuitos BGA deberán ser soldados con la misma clase de soldadura con que vienen fabricadas sus esferas.
- Para componentes discretos, somos libres de elegir durante el tiempo que demore la migración total de la industria y los consumidores, a productos libres de Plomo. El criterio particular que tengamos acerca de la toxicidad y la amigabilidad con el ambiente nos debería orientar para elegir la soldadura y los circuitos impresos correctos.